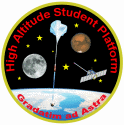

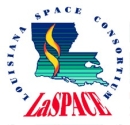

Payload 11 Information
Payload Flight Number:
Institution:
Payload Title:
High Altitude Robot Servo Motor Test
Student Leader:
Faculty Advisor:
Payload class:
LARGE
Payload ID Number:
11
Mass:
1.6kg
Current:
500mA
Serial Downlink:
YES
Analog Downlink:
NO
Serial Commands:
YES
Discrete Commands:
NO
Payload Specification & Integration Plan
Due:
Delivered:
Payload Integration Certification
Scheduled:
Actual:
Flight Operation Plan
Due:
Delivered:
Final Flight / Science Report
Due:
Delivered:
Abstract:
Our proposal focuses on the testing of critical components of the next phase of a high altitude robotic puppet that will be used on Near Space balloon missions to engage younger students (K- 6). The prototype robotic puppet has been under the development at the University of Bridgeport (UB) supported by a Connecticut Space Grant College Consortium (CSGCC) Faculty Seed Money Grant awarded to Dr. Neal Lewis (PI) and Dr. Jani Pallis (Co-PI). A multidisciplinary team of undergraduate and graduate students at the University of Bridgeport developed the robot and its existing housing and already have experience with the initial prototype robot. The scientific objectives of the HASP experiment are to test and ensure that the robot will function at high altitude and temperature for longer periods of time (in particular to test the longevity and continued functionality of the multiple servo motors used in the robot in the harsh environment of Near Space). There is concern regarding survivability/failure at low temperature and pressure, as well as continued power output at the proper level for the robot’s gestures and the continued functionality of the lubricants used within the motors under Near Space conditions. |