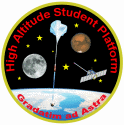

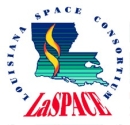

Participant Information
Call for Proposals
The HASP 2025 Call For Proposals has been released. As detailed in the CFP, the Monday September 27, 2024 Teams conference information can be optained by registering on the HASP 2025 Q&A Registration Form. If you intent to proposal for a seat on HASP 2025, a Notice of Intent is required. The NOI is due on October 11, 2024. There is a new Coversheet and Proposal Template document for this HASP season. All applicants should follow this template guideline.
HASP 2025 Call For Proposals | PDF Version |
HASP 2025 Notice of Intent | Form Link |
HASP 2025 Coversheet and Proposal Template | Doc Version |
Example HASP Student Payload Application | PDF Version |
Example HASP Student Payload Application | PDF Version |
Teams preparing a HASP proposal/payload are advised to download and read the HASP Student Payload Interface Manual as well as CSBF website postings at http://www.csbf.nasa.gov/convdocs.html particularly the FY07 User's Handbook. Also of use are the Gondola Design documents at http://www.csbf.nasa.gov/gondoladocs.html.
Student Payload Interface
HASP Payload Interface Manual | PDF Version |
There are two classes of payload seats available to students on HASP. The more numerous "small payload class are generally used for smaller experiments or testing of satellite prototypes. The "large" payload class is useful for complex, large geometry or heavy experiments. The detailed compatibility for each payload class is given below.
Small Student Payloads: | |
Total number of Positions available | up to 16 |
Maximum Weight: | 3 kg (6.6 lbs) |
Maximum Footprint (must include mounting structure): | 15 cm x 15 cm (approximately 6"x6") |
Maximum Height (may need to be negotiated with neighbor payloads): | 30 cm (approximately 12") |
Supplied Voltage: | 26-30 VDC |
Available Current: | 0.5 Amps |
Maximum serial downlink (bitstream): | 1200 bps |
Serial interface: | 1200 baud, RS232 protocol, DB9 connector |
Analog downlink: | 1 ADC Input 0 to 5 VDC |
Discrete commands: | Power On, Power Off and 1 additional command |
Analog & discrete interface | EDAC 516-020 |
Large Student Payloads: | |
Total number of Positions available | up to 8 |
Maximum Weight: | 20 kg (44 lbs) |
Maximum Footprint (must include mounting structure): | 38 cm x 30 cm (approximately15"x12") |
Maximum Height (may need to be negotiated with neighbor payloads): | 30 cm (approximately12") |
Supplied Voltage: | 26-30 VDC |
Available Current: | 2.5 Amps |
Maximum serial downlink (bitstream): | 4800 bps |
Serial interface: | 4800 baud, RS232 protocol, DB9 connector |
Analog downlink: | 1 ADC Input 0 to 5 VDC |
Discrete commands: | Power On, Power Off and 1 additional command |
(It may also be possible to negotiate up to 4 additional command pairs; i.e. F1 on, F1 off) | |
Analog & discrete interface | EDAC 516-020 |
Each student team accepted for flight on a HASP mission will be shipped either a "small" or "large" payload
mounting plate (see figure). each plate is constructed of 6 mm thick PVC with a "keep out" area marked around the
parameter and holes in each corner for bolting the plate to HASP. Within the allowed region of the plate the payload can be mounted
and wired as necessary. Also provided on the plate are DB9 and EDAC 516 connectors with wiring pigtails to provide the telemetry,
power & commanding interface. Details about the mounting plate and electrical interface can be found in the
HASP Student Payload Interface Manual.
Deliverables
If your payload is accepted, your seat on the next HASP
flight is contingent on providing documentation describing your payload as well
as your plans for integration and flight. In addition, application for the
future HASP flight will be contingent on delivery of a Final Flight Science
Report. These documents are described below and templates are available as
indicated.
HASP Monthly Status Report
HASP Payload Specification and Integration Plan
NASA Integration On-site Security Clearance Documentation
The Sample version of the Foreign National documentation required for all foreign visitors to NASA facilities can be found on this (Word Document).
NASA Flight On-site Security Clearance Documentation
The Sample version of the Foreign National documentation required for all foreign visitors to NASA facilities can be found on this (Word Document).
HASP Payload Integration Certification
HASP Flight Operation Plan
This document will detail procedures for flightline setup, pre-launch checkout, flight operations, error recovery, safeing and payload recovery including a timeline showing specific events relative to the launch at T=0 and identifying personnel participating in flight operations. Note that any operations requested to be performed by HASP flight personnel other than the power-up approximately one hour prior to launch (T - 1 hr) and power down prior to terminate must be specified in this document. (Template)
Final Flight/Science Report
A final report on the results from the flight of your payload is due by the end of the calendar year. This report should include an assessment of the payload performance, problems encountered, lessons learned as well as science / technical results from the flight. To access the final report submission form, please click on the provided link (Final Report Submission link)